Raffaele Russo will defend his PhD at the Faculty of Engineering of Bilbao, UPV/EHU
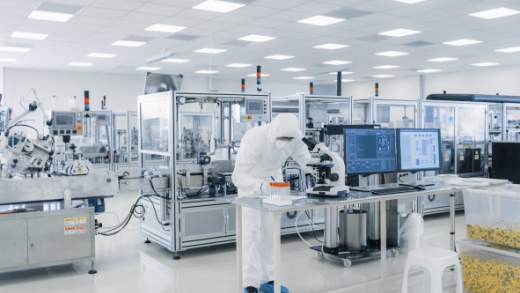
Raffaele Russo will defend his PhD at the Faculty of Engineering of Bilbao, UPV/EHU on “Cosserat thermo-mechanics under finite deformations: theory and finite element implementation”.
The PhD has been supervised by Prof. Franck Andr´es Girot Mata (UPV/EHU) and Prof. Samuel Forest (MINES ParisTech).
The PhD has been performed in the framework of the LTC ÆNIGME and the ENABLE ITN Project (H2020-MCSA-ITN Grant n°764979). “ENABLE proposes a complete rethink of the usual process simulation methods. Innovative multiscale (from microscopic to macroscopic scales), and multi-physics (strong thermomechanical and microstructural couplings) are addressed through multi-level advanced simulation.”
People can follow the defense online at:
https://ehu.webex.com/ehu/j.php?MTID=m6c347aa5eeb92b2e2b426a64891f164a
Abstract
Predicting the performance of manufactured parts is extremely important, especially for industries in which there is almost no room for uncertainties, such as aeronautical or automotive. Good quality manufacturing operation simulations are essential to obtain reliable numerical predictions of the processes. Numerical methods such as Finite Ele-ment Methods represent a powerful instrument in achieving high level of reliability of the simulations.
During most metal manufacturing processes, the medium deforms by generating large quantities of plastic strain and relatively high strain rates. Working with metals that are characterized by low thermal conductivity properties inevitably induces heat to be locally retained, thus developing high temperatures where the material deforms the most. Such particular combinations of low thermal-property material and high strain-rates-inducing manufacturing processes might lead to plastic strain localization, also known as Adiabatic Shear Bands (ASB). These are unfavorable conditions for the classical mathematical mod-els that are used to predict the behavior of the continuum, because they are not anymore able to deliver predictions that are in good agreement with experimental evidence. Under these circumstances in fact spurious mesh dependency is exhibited.
Since the first evidences of the shortcomings of the classical model were highlighted, many non-classical continuum mechanics theories have been developed to overcome this issue, and most of them introduce dependencies at different levels with the plastic strain gradient. In the first part of the manuscript, some of these theories are presented and their specific regularization properties are addressed. One option which can be used to regularize such a non-physical behavior is to resort to the micromorphic continuum.
The micromorphic theory enhances the continuum description by introducing addi-tional degrees of freedom to the body, such that its position is not the only variable that can uniquely describe the status of the continuum. In the example of the micro-morphic theory, the additional degree of freedom might be forced to coincide with the cumulative plastic strain. This manuscript includes the investigations on the extents of the regularization properties of the scalar micromorphic plastic strain gradient theory.
The cumulative plastic strain, however, is not the only field which can be used to regularize the artifacts previously discussed. In fact, we can imagine to enhance the continuum with not only one, but three additional variables, which are meant to represent the parametrized grain rotations. For such specific choice of micromorphic variable, the micromorphic theory takes the name of Cosserat theory, named after the two French Cosserat brothers. In the Cosserat theory the grain rotation is used to define a non- classical strain measure, in which the difference between material and grain rotation represents an additional deformation measure, thus inducing additional forms of stress.
The Cosserat theory represents the core of the investigation pursued during the PhD that led to the present manuscript. The theory has first been studied in its small deforma-tion framework. The effects of the characteristic lengths on the thickness of the predicted shear bands have been reported, and the simulations of the ASB formation have been carried out using such theory. Subsequently, a large deformation framework of the elasto-visco-plastic Cosserat theory has been proposed. The model has been developed under adiabatic thermomechanically-compatible assumptions, in order to cope with the condi-tions that are met during machining operations. The model has been implemented in a FE numerical software. Simple and more complex tests have been used to validate the model implementation.
Since deformation localization was the main area of investigation, specific analytical solutions of simplified localization cases have been developed under small deformation framework using the elasto-plastic Cosserat media. The analytical solutions have also been used to verify the correctness of the numerical implementation.